Process Designer is aligned with Lean, What is Lean?
- Lean = Doing More with Less
- Less Time, Inventory, Space, Labour and Money
- A way of systematically achieving profitable growth
- Systematic Elimination of Waste
- Lean – Organisation focuses on its core capabilities and devoid of any waste
- Lean Enterprise – approaches that focus on the elimination of waste in all forms
- smooth, efficient flow of materials and information throughout the value chain to obtain faster customer response, higher quality and lower costs
Process designs are subject to continuous improvement over time - Kaizen is a change for the better and it’s a cultural change! Kaizen is good change that drives improvement.
EIMS use WMS as a process to manage process! Process designer is used to create process that is widely adopted and improves efficiency and advocates lean.
Principles of Lean Thinking
There are 14 principles of Lean:
- [understand the] Purpose
- Outside-in thinking, Big Picture
- [map the right] Process
- End to end = flow as it is done today
- ^ Pull
- e.g. Order a new process using service in Storefront
- e.g. JITT - Help content so that users can do the job
- Level the workload
- Quality improvement
- Standardise
- Visual controls
- Technology
- Leadership
- Excellence
- Respect partners
- Root cause
- Slow decisions
- Learning Organisation
However designers will focus mostly on these:
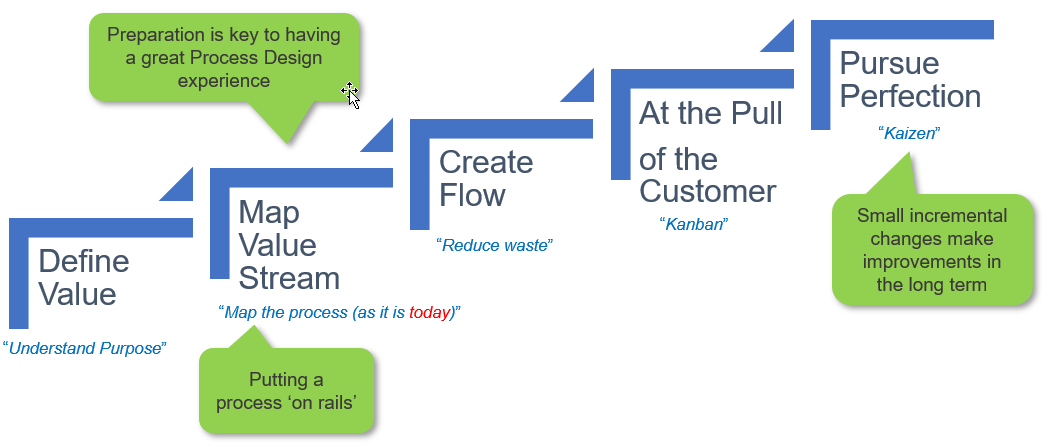
Using these principles is a state of mind!
For a designer the three most important principles to remember are:
- Understand the purpose
- Clarifies thinking and improves decision making
- Seek to understand
- Outside in thinking - Look at it through the eyes of the client: If you were the customer would you be happy to pay for what you are doing?
- Big picture - see things end to end
- the beginning of the process = customer demand (creates value/sees value)
- the end of the process = client pays for it, sees value. Client pays with a smile on their face - couldn't have gotten better value elsewhere
- Map the process
- Make the process manageable - Show not Tell
- Learning Organisation
- People who understand what they're doing and why they're doing it
- Just-in-time training (JIT)
The very first thing a process designer must do is understand the purpose - why is the process necessary and what is it for. Outside in thinking is key - Look from the eyes of the customer so that you understand your true purpose!
- Identify the value stream: how much would you pay?
Following best practice the next step is to map the process. This is a time and motion study. Which tasks add value => value stream/chain.
Map exactly what is done. Observe = Show not tell. Document exactly what is done so that you can share this knowledge with all users
- You have shadowed the most experienced users to map the process and you must ensure that the knowledge required is documented for all other users who will interact with the process Task/WorkItem in the future irrespective of their level of knowledge (new users, experienced users, super users).
- Identify what happens TODAY
-
- You can only improve a process once it is standardised